Injection Mold Makers: Crafting Precision in Metal Fabrication
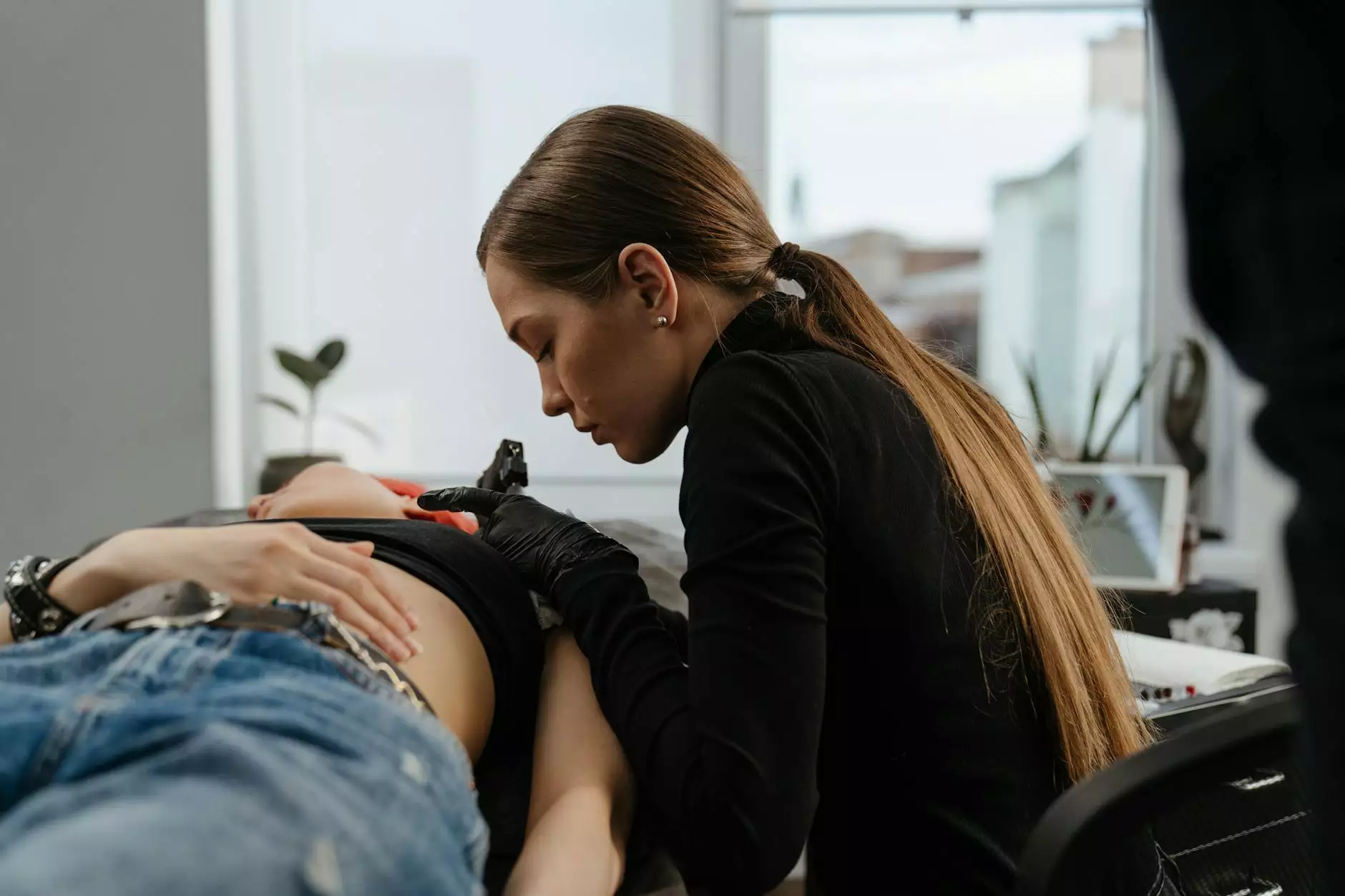
In the fast-evolving world of manufacturing, injection mold makers play a critical role that cannot be overstated. These artisans and engineers are the backbone of the plastic production industry, designing and creating molds that dictate the final shape and quality of plastic products. With advancements in technology, the realm of metal fabrication and injection molding has become more intricate and essential than ever before.
Understanding the Role of Injection Mold Makers
At the heart of effective metal fabrication lies the expertise of injection mold makers. Their primary responsibility is to produce molds capable of withstanding high pressures and flawless manufacturing processes. They utilize various materials and techniques to ensure durability and precision in each mold, which significantly impacts the quality of the final product.
The Process of Injection Molding
Injection molding is a process characterized by the injection of molten material into a mold where it cools and solidifies, thereby forming a specific shape. The role of injection mold makers is vital in this process, comprising several critical steps:
- Designing the Mold: This involves creating a detailed CAD (Computer-Aided Design) model that reflects the specifications needed for the end product.
- Material Selection: Choosing the appropriate materials for the mold is crucial; common options include aluminum, steel, and other alloys.
- Fabrication: This phase involves the actual manufacturing of the mold. Precision is key here, as even the slightest error can lead to significant issues in mass production.
- Testing and Validation: After the mold is created, it undergoes rigorous testing to ensure it meets the specifications and tolerances before going into production.
The Importance of Quality in Injection Molding
Quality assurance is a cornerstone of successful manufacturing, especially for injection mold makers. A well-made mold not only enhances production efficiency but also directly influences the quality of the end product. Factors such as dimensional accuracy, surface finish, and durability all hinge on the quality of the mold.
Factors Affecting Mold Quality
- Precision Engineering: The accuracy with which the mold is created determines the dimensional tolerances of the final product.
- Material Quality: The choice of materials used for both the mold and the injected substance affects longevity and product quality.
- Cooling Systems: Implementing effective cooling systems within the mold can significantly decrease cycle times and improve the overall efficiency of production.
- Maintenance: Regular maintenance of molds is essential to ensure they remain in optimal working condition, which directly impacts production quality.
Technological Innovations in Injection Mold Making
The field of injection mold making has not remained static. The introduction of new technologies has revolutionized the industry, making the process more efficient and cost-effective. Some of the prominent advancements include:
3D Printing
3D printing technology has emerged as a game-changer for injection mold makers. It allows for rapid prototyping and testing of molds, significantly speeding up the development process. This high-speed manufacturing capability enables designers to iterate quickly, reducing time to market.
Computer Simulation
Advanced simulation software helps mold makers predict how molten plastic will flow into the mold. This predictive capability allows for adjustments to be made before production begins, minimizing waste and enhancing production efficiency.
Automated Manufacturing Processes
Automation in mold manufacturing has led to improved precision, reduced human error, and enhanced productivity. Automated machines can work continuously, creating parts with greater consistency and at a much faster rate than traditional methods.
Choosing the Right Injection Mold Maker
When selecting an injection mold maker, it's vital to consider several factors to ensure you're partnering with the right provider:
- Experience and Expertise: Look for a provider with a proven track record in the industry. Experienced mold makers will have deep knowledge of various materials and manufacturing techniques.
- Technology Adoption: Choose a company that leverages the latest technologies in mold making, such as those mentioned earlier. This commitment to innovation often reflects the quality of their output.
- Quality Assurance Processes: Understand their quality control methodologies. A reputable mold maker should have robust testing and validation processes in place to guarantee the quality of their molds.
- Customer Service: Good communication is essential for a successful partnership. A mold maker who is responsive and values customer relationships can often lead to better project outcomes.
Applications of Injection Molding
The applications of injection molding are vast and varied, impacting numerous industries:
Consumer Products
Everyday items from containers to toys are produced using injection molding, making it an indispensable part of consumer goods manufacturing.
Automotive Industry
In the automotive sector, injection molding is employed for creating complex components such as dashboards, panels, and more, enhancing both function and aesthetics.
Electronics
Injection molded parts are widely used in electronic devices, where precision components are crucial for performance and reliability.
Medical Devices
The medical field utilizes injection molding for creating devices that require the utmost precision and adherence to quality standards to ensure patient safety.
Sustainability in Injection Molding
As industries globally seek to minimize their environmental impact, injection mold makers are also adapting. The focus is shifting towards more sustainable practices, including:
- Recyclable Materials: Utilizing recyclable materials for molding processes helps reduce waste and promote sustainability.
- Energy-efficient Processes: Implementing energy-efficient machinery and manufacturing techniques contributes to lower energy consumption.
- Waste Reduction: Innovations in mold design aim to minimize material waste throughout the production cycle.
Conclusion: The Future of Injection Mold Makers
The future of injection mold makers is bright, filled with opportunities for innovation and growth. As new technologies emerge and practices evolve, the role of these professionals will remain crucial in shaping the landscape of manufacturing. Companies like DeepMould.net are at the forefront of this industry, committed to delivering high-quality, precision-engineered solutions that meet the demands of today's market.
Investing in the right injection mold maker is not just about finding a service provider; it’s about partnering with a company that understands your vision and has the capability to turn it into reality. As industries continue to grow and adapt, the expertise of injection mold makers will be integral to driving success and innovation.