Understanding Injected Molded Plastic: Revolutionizing Metal Fabrication
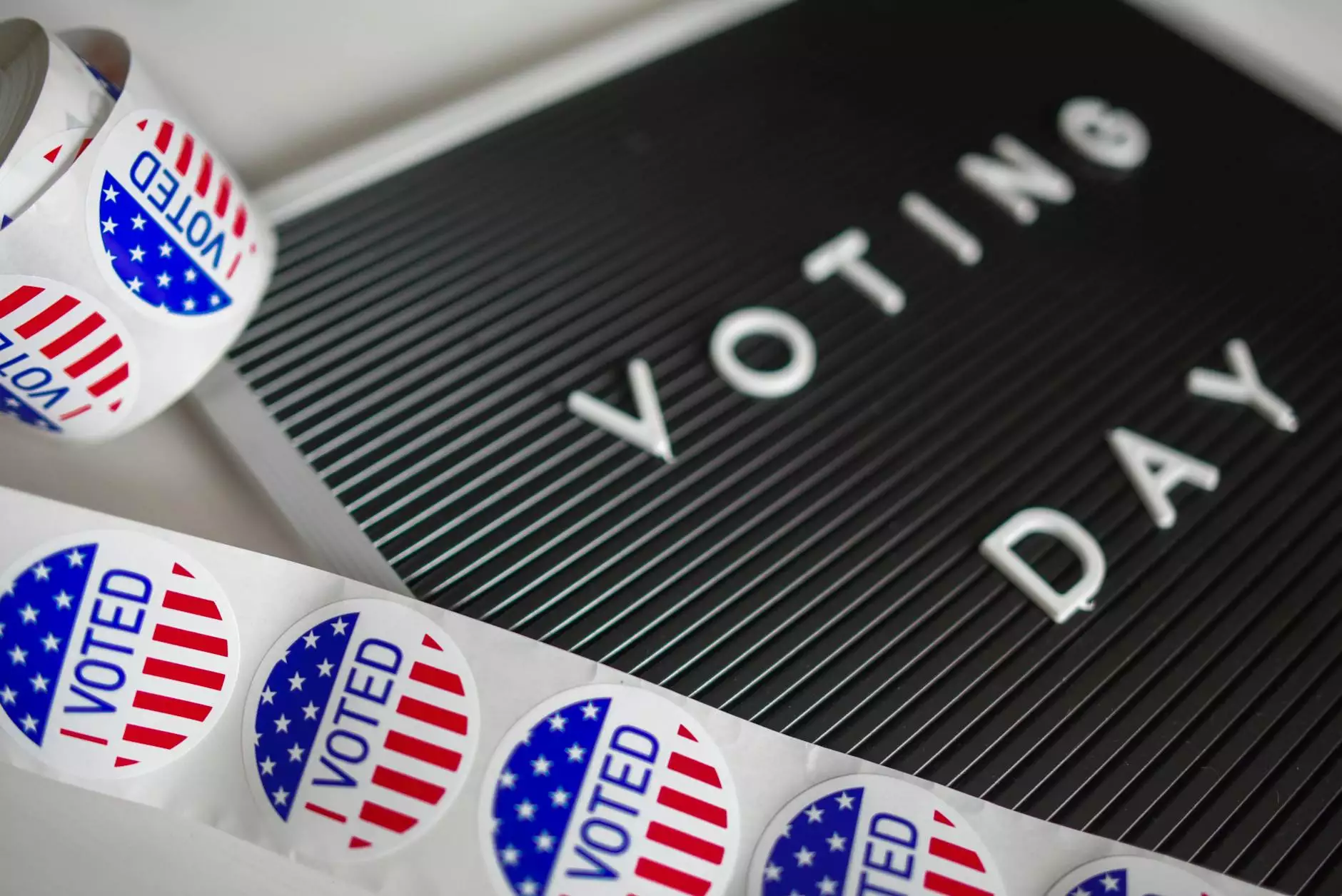
Injected molded plastic has become a cornerstone of modern manufacturing, significantly impacting various industries, including metal fabrication. This comprehensive article delves deep into the world of injected molded plastic, exploring its applications, advantages, and how it's reshaping the landscape of production. As businesses like Deep Mould evolve, understanding this technology's role is essential.
What is Injected Molded Plastic?
At its core, injected molded plastic is a manufacturing process that involves creating plastic parts by injecting molten plastic into a mold. This technique is highly versatile and allows for the production of complex shapes and designs that would be challenging to achieve with other methods.
The process typically involves the following steps:
- Material Selection: Various types of plastics, such as ABS, polypropylene, and polycarbonate, can be used based on the desired characteristics of the final product.
- Mold Creation: High-precision molds are designed and manufactured, typically from steel or aluminum, to ensure durability and longevity.
- Injection Process: The selected plastic material is heated until it becomes molten and is then injected into the mold under high pressure.
- Cooling and Ejection: After the molten plastic cools and solidifies, the mold is opened, and the finished part is ejected.
The Advantages of Injected Molded Plastic in Metal Fabrication
The integration of injected molded plastic into metal fabrication offers numerous advantages:
1. Cost Efficiency
One of the most significant benefits of using injected molded plastic is its cost efficiency. The initial investment in molds can be high, but the ability to produce large volumes of parts at a lower cost per unit quickly recoups this expense. This is particularly beneficial in industries where high production rates are required.
2. Design Flexibility
Injected molded plastic allows manufacturers to create intricate designs and shapes that may be difficult or impossible to achieve with traditional metalworking techniques. This flexibility encourages innovation in design while maintaining structural integrity.
3. Reduce Waste
The injected molding process is highly efficient and minimizes waste. Since the exact amount of plastic is injected into the mold, remnants are significantly reduced compared to other manufacturing methods. Any excess plastic can often be recycled and reused, contributing to sustainability efforts.
4. Lightweight Solutions
Products made from injected molded plastic tend to be lighter than their metal counterparts, which can reduce transportation costs and improve the overall efficiency of the final product.
5. Fast Production Times
The speed of injected molding means that prototypes and finished products can be produced rapidly. This acceleration is crucial for businesses looking to meet market demands swiftly.
Applications of Injected Molded Plastic in Metal Fabricators
In the realm of metal fabrication, injected molded plastic plays a transformative role across several applications:
1. Automotive Industry
The automotive sector is a prime beneficiary of injected molded plastic. From dashboard components to exterior trims, plastic parts offer durability and lightweight solutions that metal cannot always provide. These parts can also be designed for specific purposes, such as enhancing aerodynamics.
2. Consumer Electronics
Most electronic devices incorporate plastic components due to their insulating properties and design capabilities. Injected molded plastics are used in casings, internal structures, and connectors, improving both functionality and aesthetics.
3. Medical Equipment
In the medical field, precision and cleanliness are paramount. Components created from injected molded plastic can be tailored to meet stringent regulatory standards while providing customizable, high-quality solutions for devices.
4. Industrial Machinery
In industrial applications, replaced metal parts with injected molded plastic can reduce weight, improve safety, and lower production costs. Additionally, many industrial components are designed for ease of maintenance, which can be achieved through plastic parts.
Choosing the Right Plastic Material
The choice of plastic in the injected molding process significantly impacts the final product's performance. Depending on the application's requirements, here are some common materials used:
- ABS (Acrylonitrile Butadiene Styrene): Known for its toughness and impact resistance, ABS is widely used in consumer goods and automotive applications.
- Polypropylene: This flexible material is excellent for containers, automotive parts, and more due to its chemical resistance.
- Polycarbonate: Recognized for its strength and durability, polycarbonate is ideal for applications needing transparency and high impact resistance.
- Polyethylene: Often used in packaging and various parts due to its lightweight and flexible nature.
Innovations in Injected Molded Plastic Technology
The field of injected molded plastic is continually evolving, with several technological advancements enhancing the process:
1. 3D Printing and Prototyping
3D printing technologies allow for rapid prototyping of molds, reducing lead times and improving the design process. This capability means businesses can iterate on designs faster, leading to innovative products.
2. Advanced Materials
New composite materials are being developed that combine the benefits of plastic with the strength and durability of metal, leading to hybrid components that benefit from both materials' properties.
3. Automation and Robotics
The integration of automation within the injected molding process boosts production efficiency, leading to consistent quality and reduced labor costs. Robotics can handle tasks such as material handling, inspection, and assembly.
Challenges of Injected Molded Plastic
While the advantages of injected molded plastic are significant, certain challenges need to be addressed:
1. Initial Setup Costs
The upfront investment in molds and machinery can be substantial. However, this cost is often mitigated by the long-term savings achieved through high-volume production rates.
2. Environmental Concerns
As with any plastic manufacturing, environmental concerns regarding plastic waste and recyclability persist. However, advancements are being made towards more sustainable practices, including the use of biodegradable materials and the recycling of offcuts and scrap materials.
3. Limited Thermal Resistance
Certain plastics may not perform well under extreme heat conditions, which can limit their use in high-temperature applications. It is crucial to select the appropriate material based on the application requirements.
The Future of Injected Molded Plastic
The future of injected molded plastic in metal fabrication looks promising. As technology advances, we anticipate further developments that will improve efficiency, reduce costs, and minimize environmental impacts. The ability to innovate and adapt to changing market demands will keep injected molded plastic at the forefront of manufacturing processes.
Conclusion
In summary, injected molded plastic offers a myriad of benefits in the metal fabrication industry. Its cost efficiency, design flexibility, and rapid production capabilities make it an invaluable resource for manufacturers. As businesses like Deep Mould continue to explore this technology, the potential for innovation and efficiency will only grow.
Embracing injected molded plastic not only enhances product offerings but also positions companies competitively in an ever-evolving marketplace. Understanding and leveraging this technology will be essential for businesses seeking to thrive in the future of manufacturing.